20多年来,金宗企业一直专注于化工、涂料等机械设备的研发制造,为用户提供机械设备设计及制造、智能控制系统研发、工程设计安装等一站式解决方案,助力客户降本增效,推动数智化转型,打造安全、环保、高效、智能的未来工厂。在这里和大家分享10万吨/年液体环氧树脂生产工艺。
一、反应原理
以双酚 A(BPA)为主要原材料,合成的环氧树脂称为双酚 A(BPA)型环氧树脂,是目前产量最大、用途最广的环氧树脂,又称为通用型环氧树脂,属于缩水甘油醚型。液态双酚 A 型环氧树脂的合成方法大致有两种:一步法和二步法。目前低分子量液体环氧树脂和中分子量固体环氧树脂,一般都采用一步法工艺;高分子量环氧树脂采用二步法。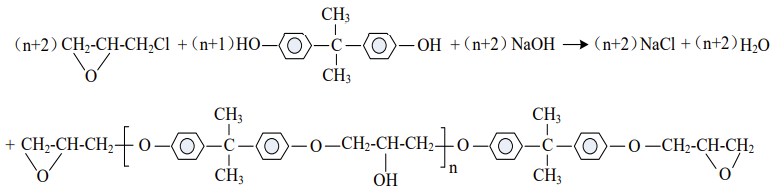
低分子量环氧树脂,采用一步法,双酚 A 和环氧氯丙烷原料在碱性条件下缩合而成。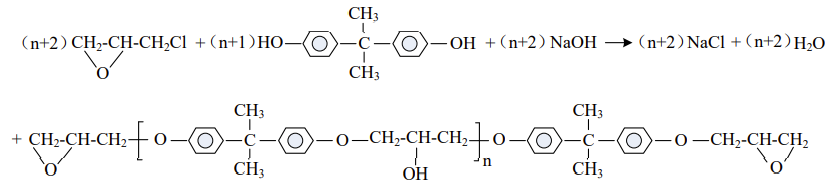
环氧树脂采用一步法工艺生产环氧树脂,一般经过预反应、主反应等过程。 预反应阶段,双酚 A 和环氧氯丙烷在碱性条件下发生开环反应,反应方程式如下: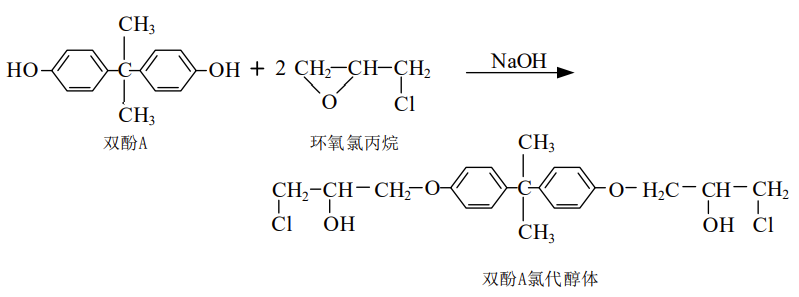
实际上,双酚 A 不完全反应成双酚 A 氯代醇体,还存在双酚 A 与环氧氯丙烷的 β 加成反应、环氧氯丙烷与双酚 A 的二次加成反应以及环氧氯丙烷的水解反应: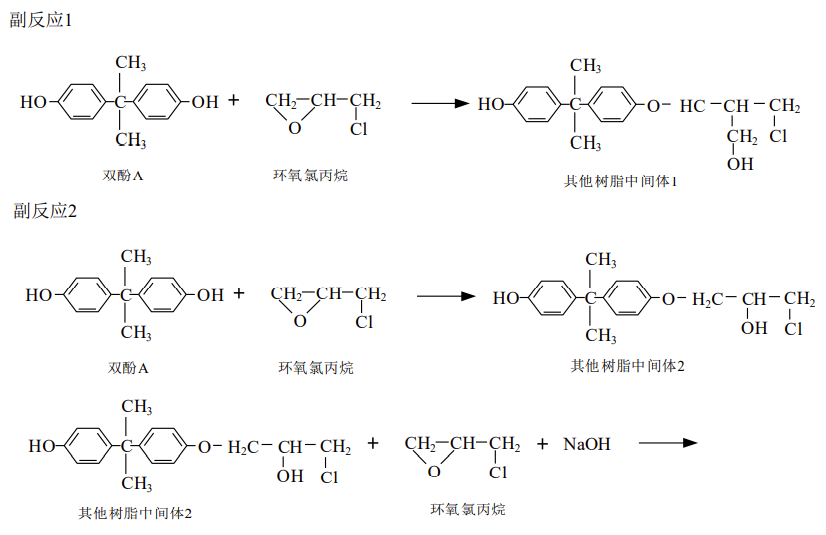
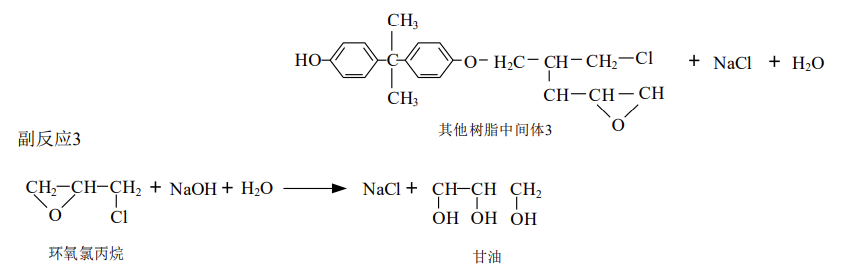
预反应阶段,环氧氯丙烷与双酚 A 质量配比为 2.09:1,环氧氯丙烷过量,考虑双酚 A 转化率为 100%,其中主反应的反应选择率为 90%,副反应 1 的选择率为 9.5%,副反应 2 的选择率为 0.5%;环氧氯丙烷发生副反应生成甘油的选择率为 0.1%。主反应阶段,双酚 A 氯代醇体与氢氧化钠发生闭环反应,反应方程式如下:
本反应段也存在副反应,副反应产生可皂化氯,它是由于双酚 A 氯代醇体脱氯化氢不充分而残留的氯根,由于该氯根比较活泼,易被微量水所水解。另外, 环氧氯丙烷在碱性条件发生水解反应,生成甘油。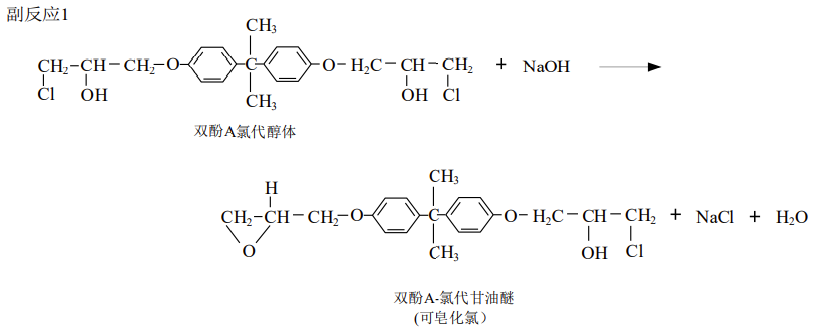
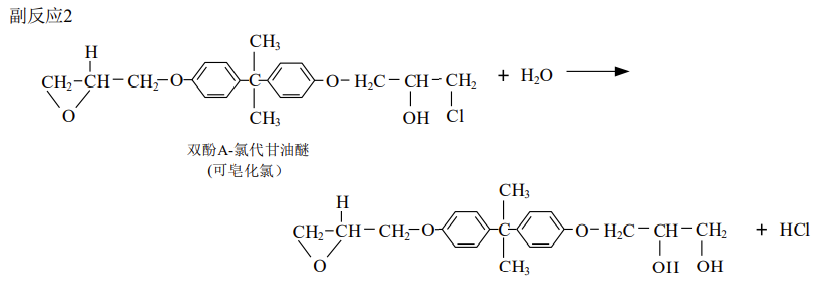
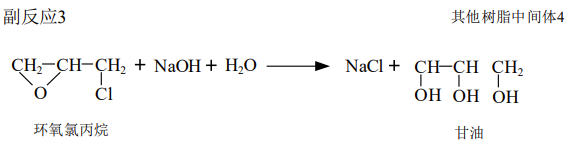
收率:以双酚 A 缩水甘油醚(环氧树脂)计收率 99%。主反应阶段,双酚 A 氯代醇体与氢氧化钠发生开环反应,考虑双酚 A 转化率为 100%,其中主反应的反应选择率为 90%,副反应 1 的选择率为 9.5%,副反应 2 的选择率为 0.5%;环氧氯丙烷发生副反应生成甘油的选择率为 0.1%。反应阶段结束后,釜内物料为环氧树脂粗产品,主要成分为:环氧树脂、未反应的环氧氯丙烷、可皂化氯、副反应生成的其他树脂中间体以及甘油、氯化钠、水等。(3)精制反应阶段 精制反应阶段,前段工序产生的可皂化氯以及其他未完全反应的树脂中间体与氢氧化钠进一步发生开环反应得到环氧树脂,以提高树脂纯度。本项目实际生产中通过统筹安排,每条环氧树脂生产线单批次可生产 11889.79kg,装置全年运行 7920h,每条生产线预计年生产 2040 批次,单条生产线产品全年总产能为 24255t,即本项目 4 条环氧树脂生产线年生产 8160 批次,基础环氧树脂产品总产能约为 9.7 万吨/年。其中 1.2 万吨基础环氧树脂需要采用 3000 吨溶剂兑稀后得到 1.5 万吨溶剂型环氧树脂。最终产品为 8.5 万吨基础环氧树脂和 1.5 万吨溶剂型环氧树脂。满足 10 万吨环氧树脂产品的设计要求。
环氧树脂生产装置运行规律及冷凝参数见表 3.2.2-1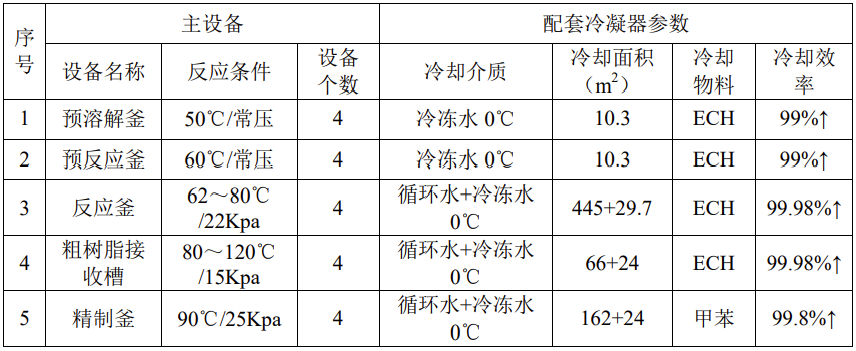
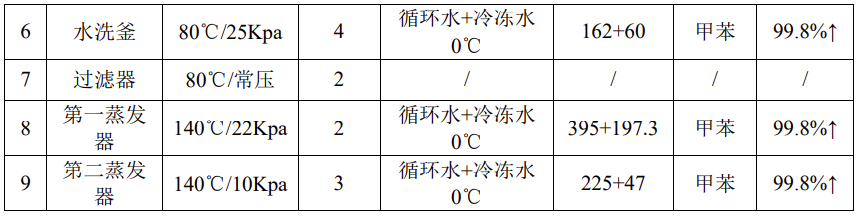
本项目环氧树脂生产工艺流程主要包括反应单元、精制单元、脱苯单元、成 品过滤及包装单元等组成。主要生产工艺流程如下:首先由行车将吨包原料送至上料工段的投料罐口,解开吨包包装底部放料口, 将双酚 A 投至投料罐,利用管链将双酚 A 从投料罐密闭输送至预溶解釜上方的加料器,预溶解釜处于微负压状态,双酚 A 由加料器密闭投加至预溶解釜。然后通过料泵将储罐区的液态环氧氯丙烷输送至预溶解釜,搅拌混合,同时预溶解釜内盘管通入蒸汽将物料加热至 50 度,保温 30 分钟后,将料液泵送至预反应釜。预溶解过程中环氧氯丙烷少量挥发,经一级冷凝(0℃冷冻水,冷凝效率 99%)后回流至预溶解釜内,未冷凝下来的环氧氯丙烷废气经管路进入环氧氯丙烷尾气回收系统。 产污环节:粉状双酚 A 在投至投料罐时,产生少量颗粒物(G1-1),经投料罐配套的收尘管路引至脉冲袋式除尘器进行处理;溶解过程产生环氧氯丙烷不凝气 (G1-2),经管道收集进入环氧氯丙烷尾气回收系统。
将预溶解釜内的物料密闭泵送至预反应釜内,通过蒸汽盘管加热将预反应釜内温度升至 60℃后,加入少量聚乙二醇作为共溶剂,再加入定量的 50%液碱作为触媒(NaOH:双酚 A 摩尔比为 0.1),在常压下双酚 A 和环氧氯丙烷进行开环反应 4h,生成双酚 A 氯代醇体,以及少量副产物等。预反应阶段结束后,釜内物料为混合液体,主要成分为:双酚 A 氯代醇体、未反应的环氧氯丙烷、副反应生成的其他树脂中间体以及甘油等。预反应釜内环氧氯丙烷少量挥发,经一级冷凝(0℃冷冻水,冷凝效率 99%) 后回流至预溶解釜内,未冷凝下来的环氧氯丙烷废气经管道进入环氧氯丙烷尾气回收系统。产污环节:预反应工段主要污染物为环氧氯丙烷不凝气(G1-3),经管道收集进入环氧氯丙烷尾气回收系统。本阶段分为 2 个操作步骤:(1)反应;(2)脱水。 打开预反应釜的底阀,将预反应釜内的物料自流进入反应釜内,在真空度 22kPa 下,将定量的 50%液碱以连续滴加的方式加入反应釜,反应温度为 60-65℃, 维持反应条件约 4 小时,NaOH 与双酚 A 氯代醇体进行闭环反应形成双酚 A 缩水甘油醚,即环氧树脂。 反应结束后,反应釜内盘管内通入蒸汽,将料温升至 80℃进行脱水,脱水时间为 0.5 小时。脱水阶段结束后,釜内物料为环氧树脂粗产品,主要成分为:环氧树脂、未反应的环氧氯丙烷、可皂化氯、副反应生成的其他树脂中间体以及甘油、 氯化钠等。其中,未反应的环氧氯丙烷在脱 ECH 段回收,可皂化氯将在精制过程进行去除,甘油、氯化钠、聚乙二醇等溶于水,将在精制、水洗阶段进行去除。反应及脱水过程,反应釜内环氧氯丙烷及水分挥发至冷凝器,通过二级冷凝 (循环水+0℃冷冻水,冷凝效率约 99.98%)后,冷凝液自流至自动分相器中,经自动分相器分离出的环氧氯丙烷环氧氯丙烷回收罐汇总,分离出的含环氧氯丙烷回收水(含 3%ECH)则进入汽提塔中进行负压蒸馏。产污环节:该环节产生的污染物为未冷凝下来的环氧氯丙烷废气(G1-4),由机械真空泵(气量 300m3 /h)排至环氧氯丙烷尾气回收系统。打开反应釜的底阀,将反应釜内的物料自流进入粗树脂接收槽内进行脱 ECH, 在真空 22kPa 条件下,利用内盘管内的蒸汽将物料由 80℃料温升温至 120℃,升温时间为 30min,过量的环氧氯丙烷转化为气体进入冷凝器中。然后通入直接蒸汽 (蒸汽压力 7kg)至物料中,保持物料温度 120~130℃,将残留的环氧氯丙烷蒸煮出来(时间约 2h),环氧氯丙烷与蒸汽进入冷凝器中。脱 ECH 结束后,釜内物料为环氧树脂粗产品,主要成分为:环氧树脂、可皂化氯、副反应生成的其他树脂中间体以及甘油、氯化钠、水等。 粗树脂接收槽内环氧氯丙烷及蒸汽挥发至冷凝器,通过二级冷凝(循环水+0℃ 冷冻水,冷凝效率约 99.98%)后,冷凝液自流至自动分相器中,经自动分相器分离出的环氧氯丙烷进入至环氧氯丙烷回收罐汇总,再回用于生产,分离出的含环氧氯丙烷回收水(含 1%ECH)则进入汽提塔中进行负压蒸馏。由于环氧氯丙烷在水中会发生水解反应,故反应段及脱 ECH 段分离出来的含环氧氯丙烷回收水呈酸性,全部回收后再经环氧氯丙烷汽提段后进入回用水槽, 最后用于精制段以中和树脂层中残留的少量 NaOH。 产污环节:该环节产生的污染物为未冷凝的环氧氯丙烷废气(G1-5),由真空泵(气量 300m3 /h)排至环氧氯丙烷尾气回收系统。由于副反应生成的可皂化氯较活泼,对环氧树脂的固化行为和固化产物等性能均有较大影响。可皂化氯被微量水水解生成 HCl,对环氧树脂固化物的绝缘性有很大影响,也是集成电路导线触点被腐蚀的原因。同时水解反应后,树脂的基端上又多了一个吸水性的羟基,使固化物的耐水性和受潮后的机械强度都会下降。因此,为避免影响产品质量,精制工段将去除可皂化氯,提高树脂纯度。精制前加入溶剂甲苯降低树脂粘度,降低树脂比重,使分液过程两相界面清 晰,容易分离。精制釜内物料静置后一般可分为三层:甲苯树脂溶液(上层)、中间物(中层)、饱和盐水(底层)。首先利用料泵将甲苯(甲苯:树脂=4:6)由储罐密闭输送至精制釜,并将粗树 脂由粗树脂接收槽泵送至精制釜,然后将精制釜抽真空至真空度约 25kPa,粗树脂溶解在甲苯溶液中,再加入 50%液碱进行精制反应去除粗树脂中的可皂化氯,以提高树脂纯度,精制反应时间约 1.5h。精制过程为负压,部分甲苯及水挥发进入冷凝器,经二级冷凝(循环水+0℃冷冻水,冷凝效率约 99.8%)后,冷凝液自流至自动分相器中,分离出的含甲苯回收水进入回收水罐,分离出的甲苯则返回精制釜。精制反应后,通入氮气使精制釜内为常压,然后再次加入甲苯和回收水溶解 反应所生成的副产物——中间物和盐。静置后,甲苯树脂溶液、中间物、饱和盐水将按上、中、下分层,打开精制釜底阀,将含盐废水排至含盐废水预处理段;中间物排入中间物罐;上层甲苯树脂溶液则转入水洗釜内进行中和、二次水洗、 再分液。脱盐过程为常压状态,考虑少量甲苯及水挥发进入冷凝器,经二级冷凝 (循环水+0℃冷冻水,冷凝效率约 99.8%)后,冷凝液自流至自动分相器中,分离出的含甲苯回收水进入回收水罐,分离出的甲苯则返回精制釜。产污环节:精制釜未冷凝下来的含甲苯废气(G1-7)由真空泵(气量 300m3 /h) 排至甲苯尾气回收系统6、水洗 水洗阶段在水洗釜内进行,分为 3 个操作步骤:水洗釜内主要将甲苯树脂溶液残存的液碱中和,并加入纯水洗去残留的 NaCl 和 NaOH,水洗釜内物料静置后一般可分为三层:甲苯树脂溶液(上层)、中间物 (中层),回收水(底层)。打开精制釜的底阀,将釜内的物料自流进入水洗釜内。在常压下,水洗釜内 盘管中通入蒸汽,将料温控制在 80℃,加入来自汽提产生的回用水(呈弱酸性) 进行对物料进行中和,中和时间约 15min。中和结束后静置 10min,物料可分为三 层:甲苯树脂溶液(上层)、中间物(中层)、中和回收水(底层)。中和回收水(底层)排至回收水罐,中间物(中层)至中间物罐。 然后再向水洗釜内加入热纯水(温度约 80℃)对物料进行水洗,水洗时间约 15min,水洗结束后静置 10min,物料可分为三层:甲苯树脂溶液(上层)、中间物 (中层)、水洗回收水(底层)。水洗回收水(底层)排至回收水罐,中间物(中层)至中间物罐。水洗完成后,将水洗釜抽真空至真空度 25kPa,利用内盘管的蒸汽保温在 80℃ 进行脱水,脱水时间为 20min。脱水过程为负压,甲苯及水挥发进入冷凝器,经二级冷凝(循环水+0℃冷冻水,冷凝效率约 99.8%)后,冷凝液自流至自动分相器中, 分离出的含甲苯回收水进入回收水罐。脱水完成后,保持釜内温度为 80℃,继续 脱甲苯,脱甲苯时间约 25min,此部分甲苯和分相器分离出的甲苯进入甲苯储罐汇总,再回用于生产。上述过程完成后,通入氮气使水洗釜为常压,将树脂甲苯溶液送至下一步进行过滤。 产污环节:该环节产生的污染物为未冷凝下来的含甲苯废气(G1-8),由真空泵(气量 300m3 /h)排至甲苯尾气回收系统。 打开水洗釜的底阀,将釜内的物料自流进入甲苯树脂溶液接收槽内。利用过滤器对甲苯树脂溶液循环过滤,以滤除细微杂质,之后将甲苯树脂溶液送脱苯段。过滤时需要向助滤器中加入助滤剂—硅藻土,此处有固体废物产生(S1-1),主要成分为树脂废渣及废硅藻土。过滤后的甲苯树脂溶液泵送至两级蒸发器,以真空蒸发方式脱除并回收甲苯。两级蒸发器脱苯条件为:一级蒸发器真空条件 22kPa、温度 140℃;二级蒸发器真空条件 10kPa,温度 140℃。连续操作。蒸发出的甲苯气体先经二级冷凝(循环水 +0℃冷冻水,冷凝效率约 99.8%)回收至甲苯储罐,不凝气经真空泵排至甲苯尾气回收系统。 产污环节:该环节产生的污染物为未冷凝下来的含甲苯废气(G1-9),由真空泵(气量 300m3 /h)排至甲苯尾气回收系统。脱除甲苯后的液态树脂,送至成品过滤段再次精密过滤,过滤后送至半成品 罐。过滤时需要向助滤器中加入助虑剂—硅藻土,此处有固体废物产生(S1-2),主要成分为树脂废渣及废硅藻土。根据生产需要,部分产品需要使用溶剂兑稀后形成溶剂型环氧树脂。不需要兑稀的产品直接进入成品罐灌装待售。兑稀、灌装装时,产生少量包装废气(G1-10), 主要污染物为甲苯,排至甲苯尾气回收系统。环氧树脂生产过程配套 ECH 汽提处置单元,主要处理来自反应釜和粗树脂接受槽产生的含 ECH 回收水,利用汽提塔将回收水中的 ECH 分离,回收水回用于水洗釜,ECH 则回用于环氧树脂生产。 流程描述:首先将汽提塔内抽真空至 15kPa,将汽提塔进料罐的料液定量 (2.0t/h)泵送至汽提塔顶部,利用内盘管的蒸汽加热至 65℃,底部料液在塔内形 成蒸汽,对从顶部进入的料液进行汽提。水和 ECH 蒸发至冷凝器,通过二级冷凝 (循环水+0℃冷冻水,冷凝效率约 99.98%)后,冷凝液自流至自动分相器中,经自动分相器分离出的环氧氯丙烷进入至环氧氯丙烷回收罐汇总,再回用于生产, 分离出的回收水则进入汽提塔底水槽,回用至水洗釜中和段。 产污环节:该环节产生的污染物为未冷凝下来的环氧氯丙烷废气(G1-6),由真空泵(气量 300m3 /h)排至环氧氯丙烷尾气回收系统。环氧树脂生产过程配套中间物处置单元,主要处理来自精制釜和水洗釜产生的中间物。利用甲苯将中间物中的树脂进行萃取回用于生产,产生的树脂废渣为危废,委托有资质的单位进行处理。通过类比,中间物的组成如下表所示。
首先将中间物罐的物料用泵输送至萃取罐,加入甲苯对中间物进行萃取,搅拌 5min 后静置,物料可分为三层:甲苯树脂溶液(上层)、中间物(中层)、含甲苯回收水(底层),然后将甲苯树脂溶液(上层)利用泵抽至回收树脂罐。连续萃取三次,中间物中的树脂基本萃取完成,萃取出的甲苯树脂溶液抽至回收树脂罐, 然后回用于精制釜内。 萃取结束后,加入直接蒸汽将物料蒸煮至 100℃,甲苯及水挥发进入冷凝器, 经二级冷凝(循环水+0℃冷冻水,冷凝效率约 99.8%)后,冷凝液自流至自动分相器中,分离出的含甲苯回收水进入回收水罐。萃取罐中剩余的料液则自流进入离心机进行离心分离,分离出的残渣(S1-4)作为危废送有资质单位处理,分离出的回收水进入回收水罐。 产污环节:此环节蒸发出的水和甲苯进入冷凝器中,未冷凝下来的甲苯不凝 气(G1-11)进入甲苯尾气回收系统,分离出的残渣(S1-3)作为危废送有资质单位处理。环氧树脂的生产过程中,在精制段脱盐操作完成后将有高盐废水产生。其主要成分为 NaCl 水溶液,呈碱性。含盐废水水质特征如下表所示。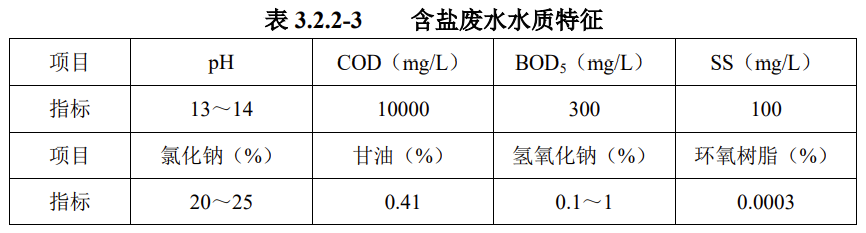
本项目配套盐水预处理单元及脱盐单元用于生产蒸发结晶钠盐。首先利用甲苯将含盐废水中的树脂萃取后回用于生产,废水再经闪蒸蒸发器蒸出甲苯及水分, 剩余的高盐浓缩废水则进入蒸发结晶车间进行蒸发结晶,蒸发结晶产生的钠盐则 经过流化床干燥后得到钠盐,蒸发出的水则经冷凝后排入污水预处理站采用“高效厌氧反应器+活性污泥法+接触氧化法”处理,然后排入集聚区污水处理厂深度处理。将精制釜产生的饱和盐水(水温约 70℃)排至含盐废水预处理单元的废水分离槽,加入甲苯对盐水中的树脂进行萃取,然后静置 10min,物料可分为两层:甲苯树脂溶液和与甲苯互溶的少量盐水(上层),盐水(下层)。利用泵将上层料液抽至回收水罐。下层盐水则进入废水接收罐,经过滤后进入闪蒸蒸发器。向闪蒸蒸发器内通入直接蒸汽,将物料蒸煮至 100℃,甲苯及水挥发进入冷凝器,经二级冷凝(循环水+0℃冷冻水,冷凝效率约 99.8%)后,冷凝液自流至自动分相器中, 分离出的含甲苯回收水进入回收水罐。闪蒸器内剩余的高盐浓缩废水进入清液罐, 送至脱盐工段,甲苯经冷凝后回至回收水罐。 产污环节:该环节产生的污染物为未冷凝下来的甲苯废气(G1-12),由真空泵 (气量 300m3 /h)排至甲苯尾气回收系统;过滤时产生过滤废渣(S1-4)。含盐废水预处理后产生高盐浓缩废水,由清液罐泵送至厂区蒸发结晶车间进行蒸发结晶处理。流程主要分为:前处理段、结晶系统。 将来自于主装置车间的高盐浓缩废水排至蒸馏槽,在真空的条件下通入蒸汽, 并通过热交换器将物料加热到过热状态,在蒸发罐内产生大量的气化蒸气,将其中所含溶剂及部份水脱除,经二级冷凝(循环水+0℃冷冻水,冷凝效率约 99.8%) 后,冷凝液自流至自动分相器中,分离出的含甲苯回收水进入回收水罐。蒸发罐内的物料被浓缩,同时形成 NaCl 结晶。盐水先经真空脱溶剂设备(65℃),再次将其中残余微量溶剂及部份水回收使用。盐水储存于结晶罐入料暂存槽,然后再利用多效结晶罐,逐步将盐水浓缩,当比重达到设定值,即送至离心机脱水,脱水后再送至干燥机干燥。产污环节:该环节产生的污染物为工艺废水(W1-1),排入污水预处理站采用 “高效厌氧反应器+活性污泥法+接触氧化法”处理后排入集聚区污水处理厂深度处理;离心机分离出蒸发结晶钠盐(S1-5)。 来自离心后的块盐由皮带机输送到流化床干燥器,流化床利用蒸汽预热的空 气热风进行干燥,得到蒸发结晶钠盐。干燥后的钠盐输送到振动筛分机将其中的块状或片状钠盐进行筛分,之后包装运输至蒸发结晶钠盐仓库。产污环节:钠盐干燥过程产生的废气(G1-13),主要污染物为颗粒物,筛分及包装产生废含尘废气(G1-14),以上废气经两级旋风除尘器+湿式除尘后,经 25m 高排气筒排放,湿式除尘器介质采用含盐废水,去除粉尘的同时回收烟气热量, 返回干燥工序,不外排。本项目环氧树脂工艺流程及产污环节见图 3.2-2。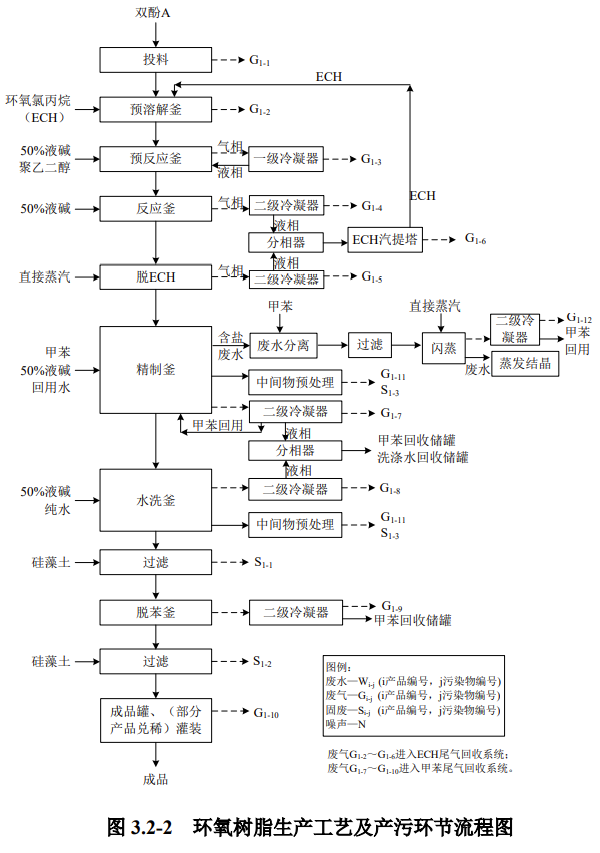
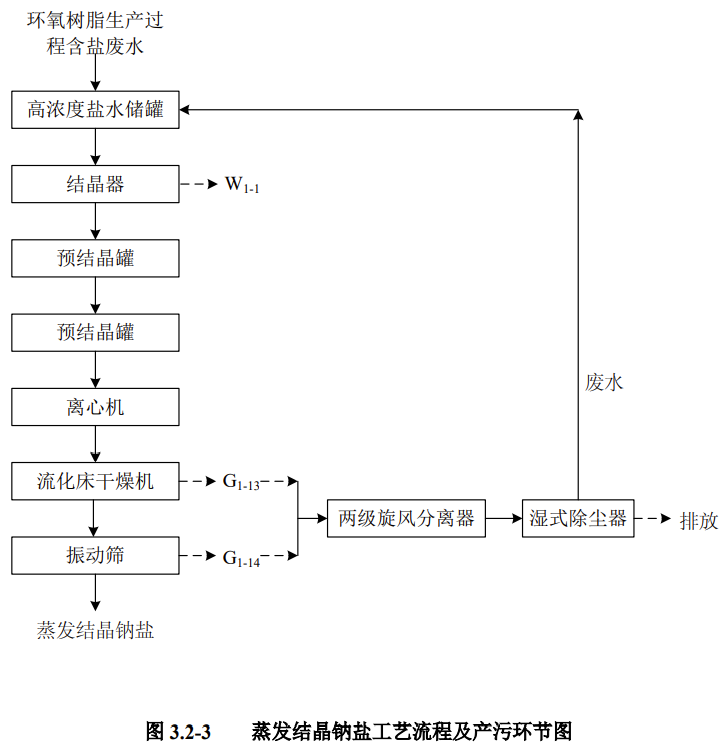
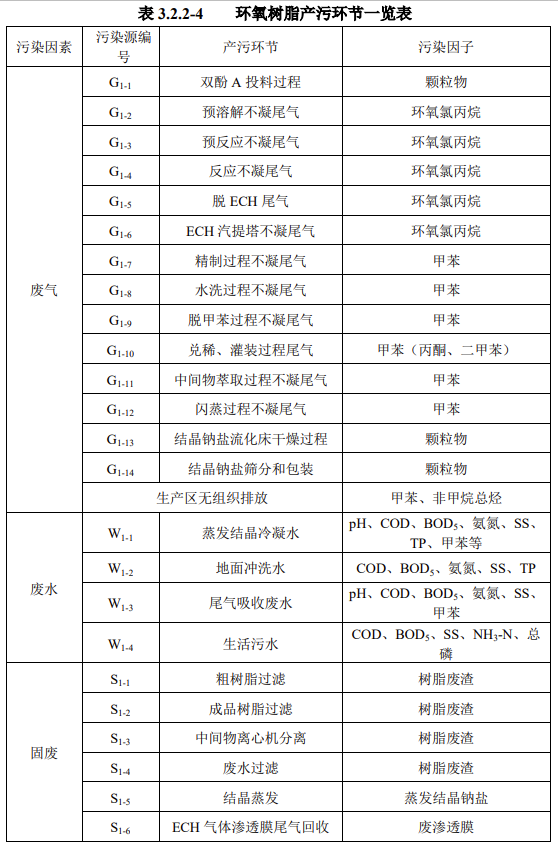

本项目实际生产中通过统筹安排,每条环氧树脂生产线单批次可生产 11889.79kg,装置全年运行 7920h,每条生产线预计年生产 2040 批次,单条生产线产品全年总产能为 24255t,即本项目 4 条环氧树脂生产线年生产 8160 批次,产品总产能约为 9.7 万吨/年,部分产品兑稀后形成 10 万吨/年的生产规模。环氧树脂物料平衡表见表 3.2.2-5,环氧树脂物料平衡图见图 3.2-4。

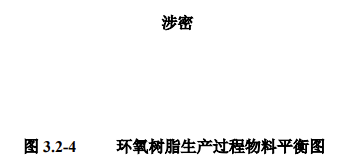
蒸发结晶钠盐物料平衡表见表 3.2.2-6,蒸发结晶钠盐物料平衡图见图 3.2-5。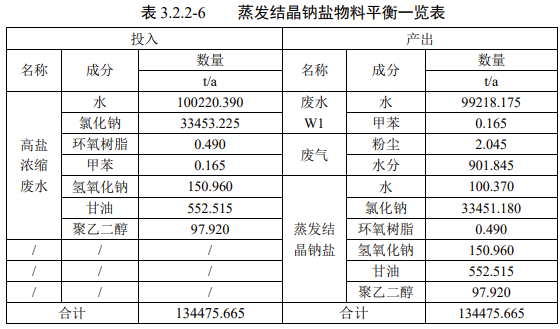
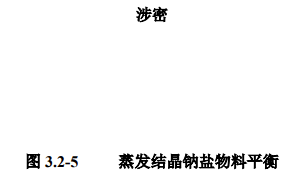
环氧树脂生产线 ECH 平衡见表 3.2.2-7,ECH 平衡图见图 3.2-6。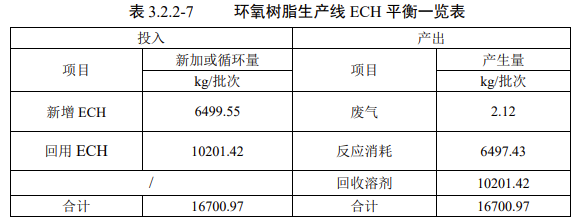
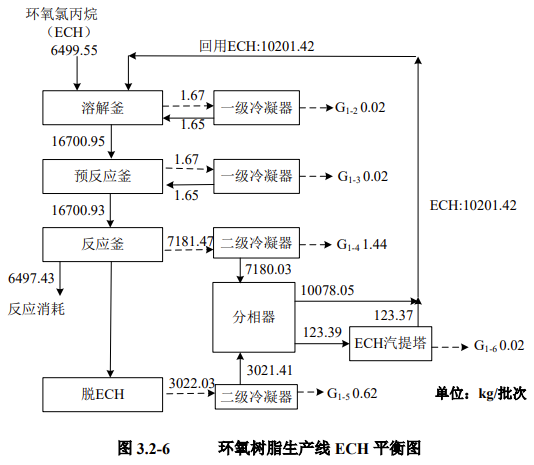
环氧树脂生产线甲苯平衡见表 3.2.2-8,甲苯平衡图见图 3.2-7。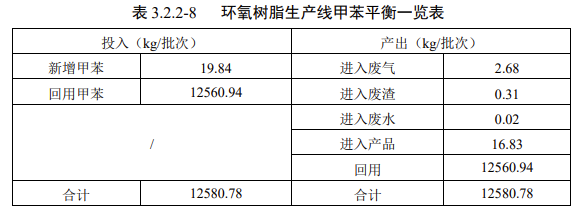

环氧树脂生产线氯平衡见表 3.2.2-9,氯平衡图见图 3.2-8。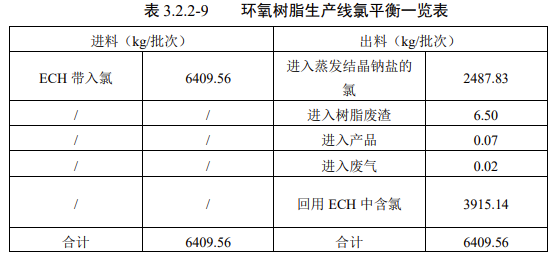
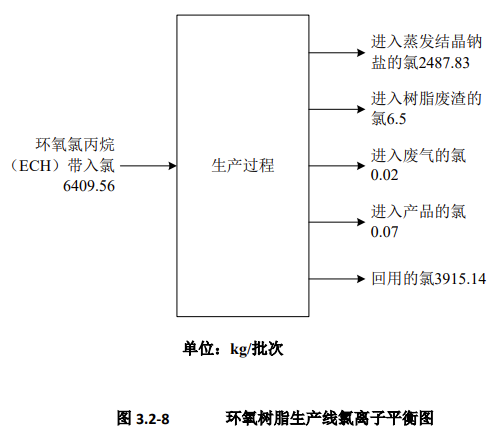
环氧树脂生产线水平衡见表 3.2.2-10,水平衡图见图 3.2-9。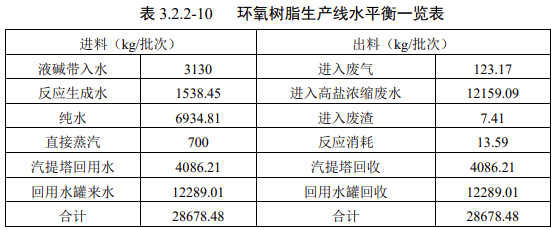
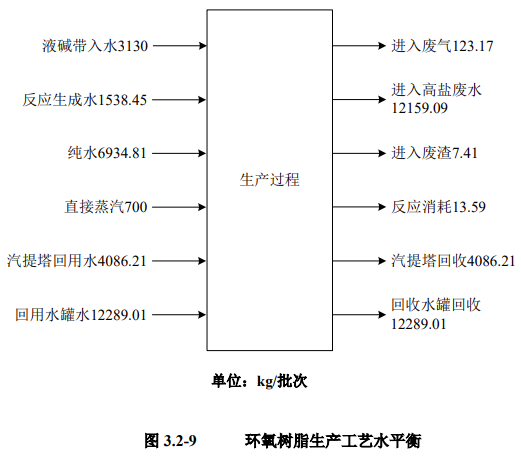